Plane colloidal mills
Plane Colloidal Mill
The rate and quality of dispersion block copolymers in bitumen depend on many parameters including e.g. polymer particle morphology and bitumen grade and constitution. Most decisive, particularly in determining the dispersion rate, is the effectiveness of the mixer involved. To get good quality products the temperature should not exceed 185°C and the blending time should be as short as possible consistent with there being sufficient time to dissolve the polymer completely in the bitumen. Before defining what criteria a good mixer should be judged by, this technical bulletin describes the basic mechanism involved in dispersion.
When the polymer is added to the hot bitumen, the latter immediately starts to penetrate into the polymer particles. Under the influence of the shear of the mixer the swollen polymer becomes mobile and disperses in the bitumen.
From this general description three parameters can be identified which mainly govern the dispersion rate of a particular copolymer.
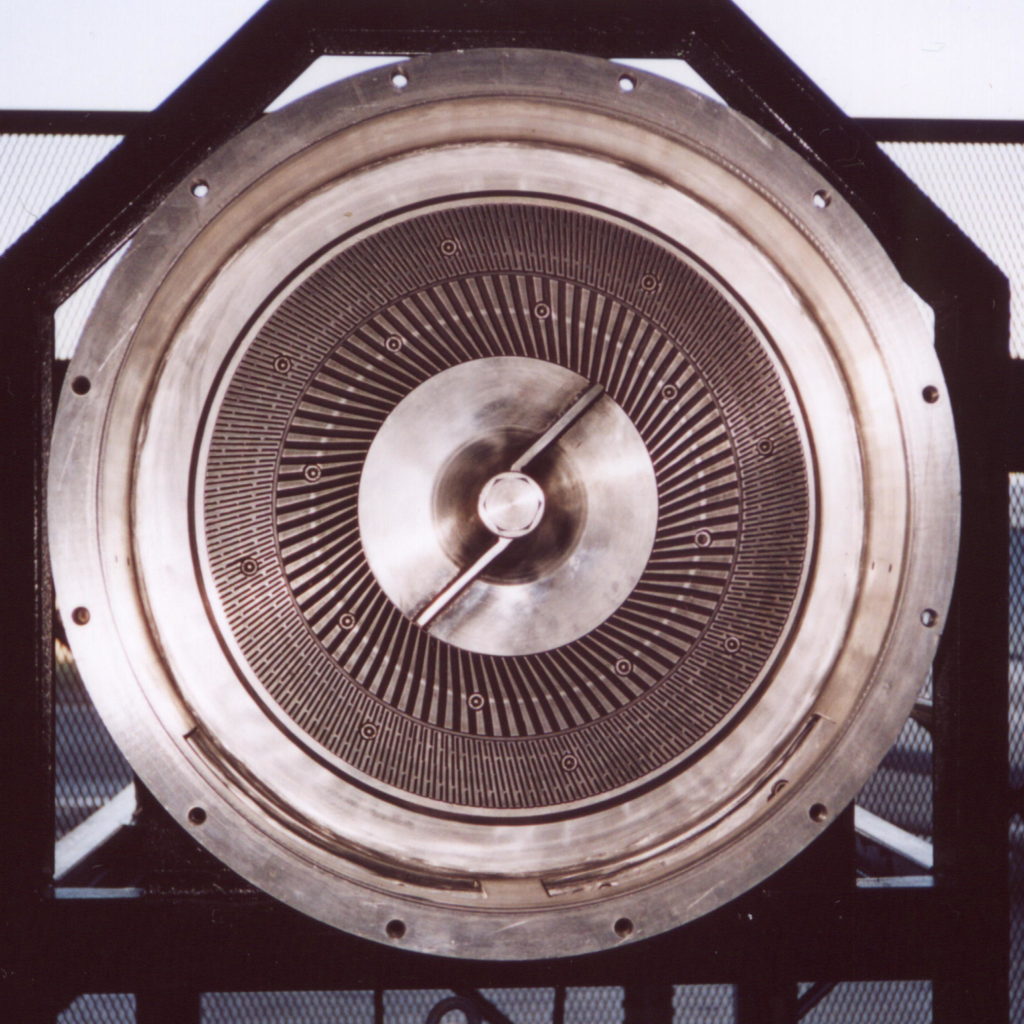
Mixers for Polymers - Asphalt Emulsion Blends
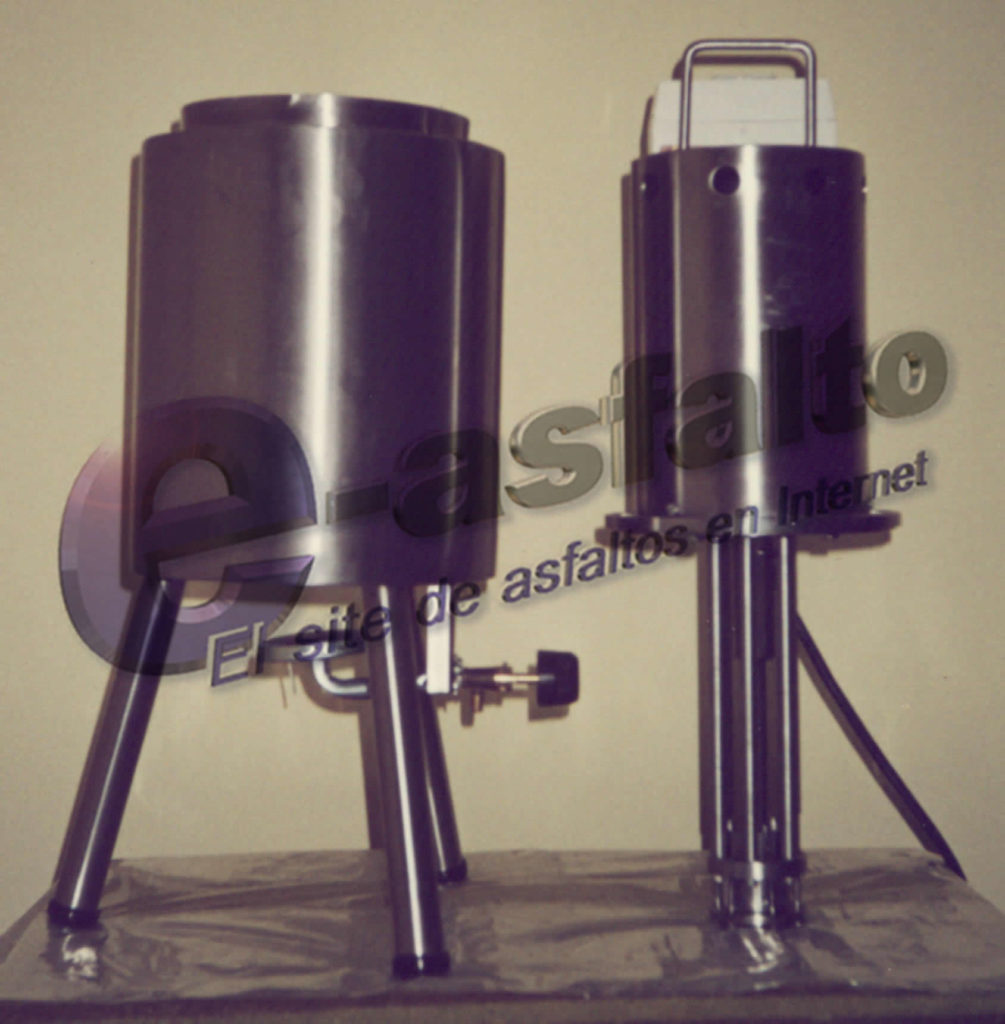
Mini Plant Model 9 liters Capacity model registered ©
– The polymer particle size at the stage of bitumen penetration: the smaller the particle size, the larger the surface area, and the more rapidly, the polymer will be penetrated by the bitumen.
– The shear exerted upon the particles after they have swollen sufficiently for the molecules to become mobile. This effect however, is less important than the particle size.
– The temperature since the diffusion rate of the penetration bitumen; which increases as the temperature rises, determines when shear becomes effective.
The first condition to be satisfied when blending bitumens and polymers is that the polymer particles should be small. This can be done by grinding the granules into powder before their addition to the bitumen, or they can be disintegrated after addition to the bitumen by using mixers in which the bitumen acts as a lubricant in a “wet” grinding process.
gap-wid th
the diameter of the rotor
the angle at which the teeth are positioned
rotation speed
number of teeth on the rotor and stator
the flow rate
A study of inmersion mixers and miners with serrated rotors and stators, has shown that the latter are capable if giving the best results. This is due to their higher rotation speed and much greater number of teeth, which together give a higher frequency of cutting action on the granules.
It has also been found that the elapsed time between polymer addition and actual grinding (pre-blending time ) is important. Long pre-blending times soften the polymer granules and may make them less easy to cut. It depends on the internal construction of the rotor and stator whether soft or hard granules are preferred for optimum disintegration. After “wet” grinding the swollen particles, the process continues with further penetration of the polymer. The shear in the mixer, which eventually mobilises the polymer molecules, is directly related to the velocity of rotation and to the viscosity of the bitumen, and is inversely proportional to the gap-width.
On the other hand the flow rate rises as the gap-width is increased and therefore, after desintegration, the dispersion process seems to become less dependent on the gapwidth. This hypothesis is strongly supported by production trials, where gap-width had no influence on total blending time. Thus overall operatiou may be best when a small gap is used to start with followed by a wider gap later. An additional benefit is that this would use less lower is the later stages.
From the above, the ideal mixer would be one which grinds the polymer granules very finely and provides high-shear followed hy high flow rates after grinding. The machinery should be powerful and soundly constructed and the grinding tools wear-resistant.
Mixers with toothed rotors and stators are most likely to satisfy these demands and can be recommended for blending polymer and bitumen. The greatly increased throughput rates and the ability to use granular forms of plymer more than compensate for their higher cost when compared with the paddle mixers traditionally used by the industry.
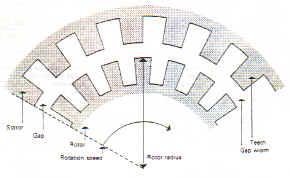