Former membran roofing
Waterproof Felts
Consist of a fibrous felt which is impregnated and/or coated with bitumen. Traditionally, the felt was made from the waste rags of wool, cotton or linen but more recently these have been replaced by cheaper materials such as wood fibre, jute, manilla hemp or waste paper. Glass fibre is increasingly used and holds up to 50 % of the market in certain countries.
Synthetic fibre felts (low-density polyethylene, polypropylene, polyester, acetylated polyvinyl alcohol, sometimes reinforced with glass fibre) are also used; their main advantage is a much greater resistance to rupture when stretched by 5 % or more as a result of movement of the roof. They also have a greater tensile strength and resistance to rotting than conventional felts but they are more expensive and may be sensitive to thermal damage during manufacture.
Depending on the type of felt, the manufacturing processes can consist of as many as three steps:
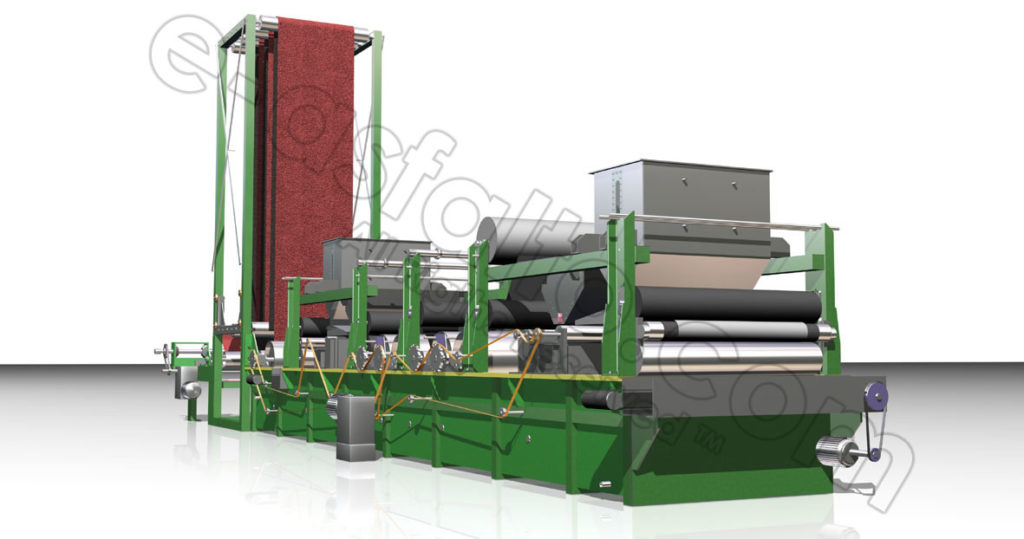
Saturating - Rotproofing - Coating

Saturating
If the felt is of an absorbent type, that is, most types made from natural fibres, it will contain up to 7% m of water even when it appears to be dry. It may therefore need drying before it is treated with bitumen. Felt is saturated by passing through a tank of hot bitumen. It may be passed over a series of rollers in the tank to increase the residence time and aid impregnation; it may also be sprayed with bitumen before entering the tank.
Another technique is to apply hot bitumen by means of rollers to one side of the felt before it enters the tank and so drive any water out of the felt to reduce foaming. The bitumen in the tank is at such a temperature to produce a viscosity of less than 200 cSt, this corresponds to 160-170°C for the usual grades ( 80/ 100 or 180/200 pen). Substantially higher temperatures of about 200°C giving viscosities down to 20 cSt are sometimes used in order to reduce residence time and so increas throughput. If foaming in the tanks is experienced, a few ppm of a silicone anti-foam agent should be added to the bitumen.

Coating
The felt (saturated, unless it is a non-absorbent glass or synthetic organic fibre type) passes directly to the coating process. Coating may be achieved by passing the felt through a tank, but pouring bitumen onto the felt or application via rollers is more usual. Speed, roller spacing (when transfer rollers are used) and bitumen temperature are adjusted to control the coating thickness. Coating viscosities are typically 200-500 cSt for thin coats and 500-1000 cSt for thicker coats, giving coating temperatures varying from 170 to 240°C depending on the grade of bitumen. Lower temperatures (higher viscosities) are used to give thick coats – a typical figure is 140°C and an extreme case is known of coating at 120°C with a bitumen containing 25% m of filler to give a thick welding felt (about 8 mm). The upper surface of the felt is sometimes coated with a thicker layer of bitumen than the lower surface.
Includes 30 to 45% m of filler (slate dust or limestone) in the coating bitumen. The coating is usually dressed with a finely divided light coloured mineral (sand, mica, talc) to prevent adhesion when rolled and to reduce the surface temperature in service by reflection of sunlight. Mineral granules, sometimes artificially coloured, are also used for aesthetic reasons and to increase durability.
The coating bitumen should have a high softening point to avoid flow under hot sunshine a value 40-50°C higher than the maximum service temperature is desirable. The penetration must not be too low, so that the felt can be unrolled without cracking. Precise limits are not known but values above 20 are usually found to be satisfactory.
Also requires an upper limit on the Fraass breaking point of the coating grade because they think that it correlates with cracking when unrolline. Typically maximum Fraass values of -18°C are required by the industry.
These requirements can only be met by blown grades of bitumen, and indeed the more highly blown the bitumen, the more combination of high softening point, high penetration and low Fraass can be obtained. For coating non-saturated felts (e.g. glass fibre), high PI grades such as 85/40 or 1 10/30 are usually used.
The most widely used coating grades are 85/25 in temperate climates and 115/ 15 for tropical service.
A large number of other blown grades have also been used to meet specific requirements, like 75/30, 85/40, 90/40, 95/25, 95/30, 95/40, 100/25, 100/40 and 110/30. In recent years, there has been a tendency to use the higher PI bitumens for the following reasons,
* The desire for a ‘multigrade’ bitumen, suitable for a wide range of service temperatures;
* A trend to thicker coatings, which require a blown bitumen of higher softening point to resist flow. The thicker coatings in turn are due in part to:
a) the greater use of glass-fibre felt which, at equal total weights, contains more bitumen than rag felts
b) the use of two instead of three layers of felt in a built-up roof
* The increasing use of roof insulation which causes a greater temperature variation in the felt.