Conical colloidal mills
Emulsion definition
An emulsion is a dispersion of two immiscible fluids in each other generally prepared using a product called an emulsifier or an emulsifying agent. Bitumen emulsification consists in dividing it into fine electrically-charged particles provided with an inter-repelling capacity.
Components

Bitumen
Bitumen is produced by petroleum refineries. An additive facilitating emulsification and improving stability and adhesion qualities is usually incorporated by the refinery before the bitumen is delivered.
Diluents and fluxes
Diluents are generally produced by the petroleum refineries. Diluents are low viscosity (0/1 or 10/15) used to fluidize bitumens. Fluxes are generally coal tar oils.
Water
The selected water must contain a minimum amount of mineral and organic impurities. In general, it is necessary to “ion exchange”, the water, using an appropriate device, to manufacture certain emulsions. Ion exchange consists of replacing the magnesium and calcium ions contained in the water by added sodium ions. In fact, magnesium and calcium ions tend to react, in particular, on CnHm-COONa type emulsifiers to form compounds insoluble in water which no longer have emulsifying properties.
Emulsifiers (or emulsifying agents)The commonly used emulsifiers are amine class chemical products. In particular, they are characterized by their liquid or paste-type consistency which affects handling, storage and dosing.AcidAs emulsifiers are insoluble in water, it is necessary to convert them into salts so as to dissolve them in the dispersing phase. To this end, they are reacted with an acid, more often than not, hydrochloric acid, in a 20-22° Baumé solution.
Manufacture parameters
Dispersion energy
Emulsion dispersion is caused by mechanical energy and physicochemical energy.
The mechanical energy divides the bitumens into fine particles and the emulsion fineness increases with the fractioning capacity.
The physicochemical energy provided by the emulsifier must:
* reduce the interfacial tension between the hydrocarbon phase and the aqueous phase so as to facilitate emulsification.
* create a protective film around the particles.
Component viscosity and temperature
In order to enable the hydrocarbon binder to properly disperse in the aqueous phase it is necessary for its viscosity to be relatively low. The optimal viscosity is 200 centipoises which is obtained by maintaining the binder at a temperature which is a function of its penetration grade. This temperature is approximately as follows:

Penetration
180/220
80/100
40/50
Emulsification temperature
140ºC
150ºC
160ºC

If you significantly exceed these temperatures, unwanted and undesirable effects may occur. In fact, if at the mill outlet, the emulsion – which is at atmospheric pressure is at a temperature greater than 95°C it “boils overs”. Nonetheless, manufacture of the aqueous phase requires that the water be at a tempeature of around 40°C and therefore it is necessary that the binder temperature does not exceed a certain limit.
There is one simple rule – which is mainly vallid for 60% emulsions – and that is that the sum of the aqueous and hydrocarbon phase temperatures does not exceed 200°C. Some emulsions must be manufactured under a pressure of a few bars to satisfy the mandatory parameters corresponding to the components and simultaneously prevent boiling of the aqueous phase.
Component dosing
Component dosing must be extremely precise, especially the emulsifiers and the acid: a variation, even very slight, may have far reaching consequences.
Dispersing phase preparation installation
The bitumen emulsion dispersing phase consists of water and various emulsifying agents which make up, more often than not, an amine hydrochloride for the cationic emulsions. Depending on the manufacture mode adopted, the dispersing phase is:
* either in one operation: the emulsifiers and the acid are added to the water at their exact dose,
* or in two operations:
• manufacture of a concentrated product by adding emulsifiers and acids at a high dose rate to the water.
• dilution of this concentrate in hot water at emulsion manufacture time at a proportion corresponding to the final dosing.
To prepare the dispersing phase, the manufacture plant is provided with the following installations:
* dosing (by weight or by volume)
* mixing and diluting, if necessary
* water heating
Certain plants are provided with a pH meter so as to be able to continuously check the compliance of the pH indicated and the one given by formulation, during the dispersing phase manufacture and then the emulsion phase manufacture.
The dispersed phase may be:
* either pure bitumen
* or a blend of bitumen in predefined proportions with:
• a flux or a diluent
• other agents, for example elastomers (this concerns modified bitumens)
Also, in certain cases, the emulsifier is fully or partly incorporated with the bitumen prior to it being emulsified. These various dispersed phase compositions require equipment whose sophistication may vary from a simple -in-line- dosing/mixing installation to a costly high-performance mixer installation.
Emulsifying equipment
Industrial manufacture of emulsions uses custom-made equipment providing thorough mixing capacities to provide varying fineness and stability dispersions. Colloid mills are usually used to manufacture emulsions. Manufacture may also be by gradual enriching of the dispersing phase.
There are various other types of colloid mills and their main characteristics are:
* an adjustable or fixed air gap between the rotor and the stator. The air gap spacing has a direct effect on the emulsion fineness.
* rotation speed which affects the size and distribution of the bitumen particles. At certain critical speeds, decantation phenomena occur causing a reduction in emulsion quality.
These colloid mills operate continuously and they are fed with the dispersing and dispersed phases by adjustable flowrate pumps.
Certain bitumen-based emulsions have special characteristics and must be manufactured under pressure in specially designed colloid mills. Equipment adapted to this special emulsifying mode must be provided upstream and downstream.
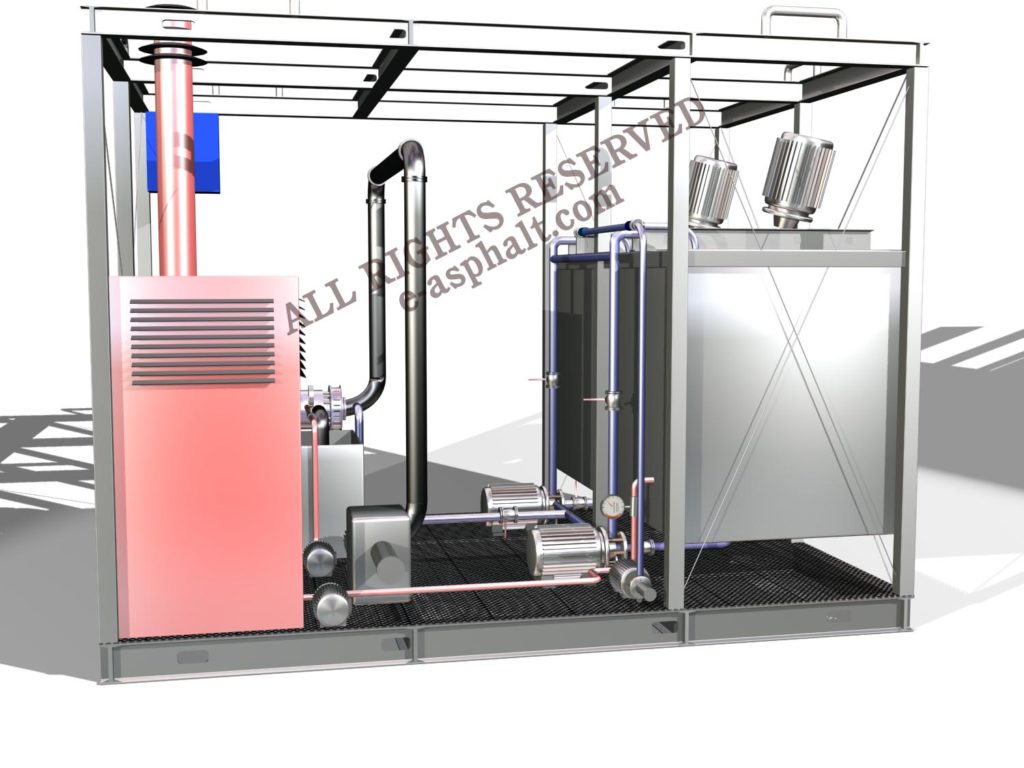
Bitumen emulsion delivery station
Generally speaking, a plant stores the emulsions it manufactures and therefore it must have the tanks and equipment corresponding to storage requirements. However, for certain special manufacture runs in limited quantities, it is preferable to directly load the emulsion in the transporter carrying the emulsion to the job site. For bulk delivery, a plant is provided with an appropriate number of loading stations corresponding to its specific requirements which are all provided with the safety devices scheduled by the legislation in force. Emulsions are less and less frequently packaged in drums. Nonetheless, to satisfy this requirement, the plant is provided with a drum installation and whenever necessary, a drum cleaning plant.